Management and conservation of personal protective equipment has been a collaborative effort to ensure we are supporting our front-line caregivers.
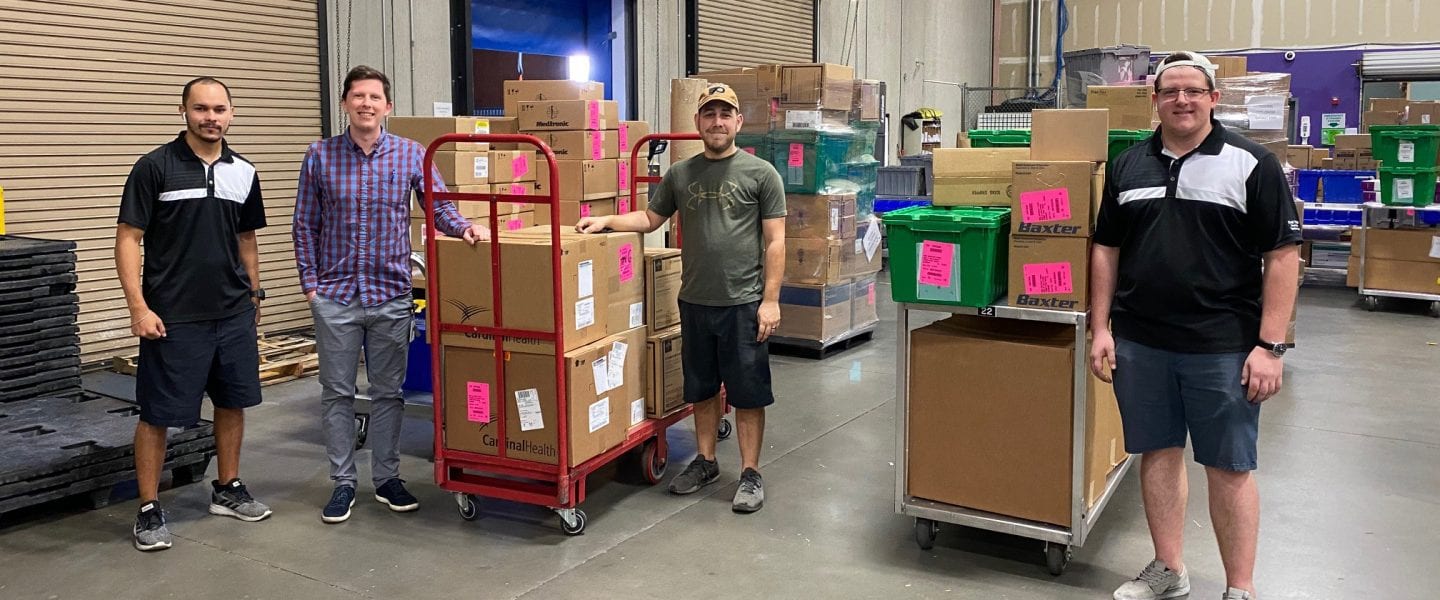
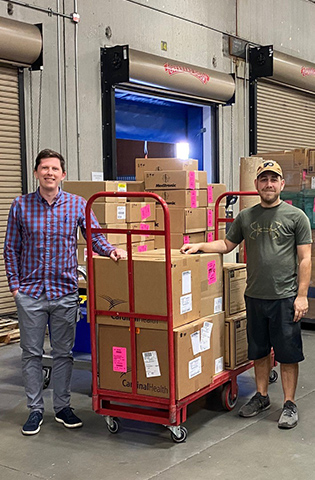
In the incredibly important world of supply chain, three disciplines loom large in ensuring that a health system runs smoothly: procurement (acquiring items efficiently and at the right price), management (taking care of those items and making sure they’re stored and utilized properly) and distribution (efficiently getting items to where they’re needed, on time). With the onset of the pandemic, a fourth discipline, conservation (managing the sustainable use of products to ensure their availability amid scarcity) is added to the equation. For us, conservation is a necessity driven by a shift in global demand for personal protective equipment (PPE) coupled with shortages of these critical supplies.
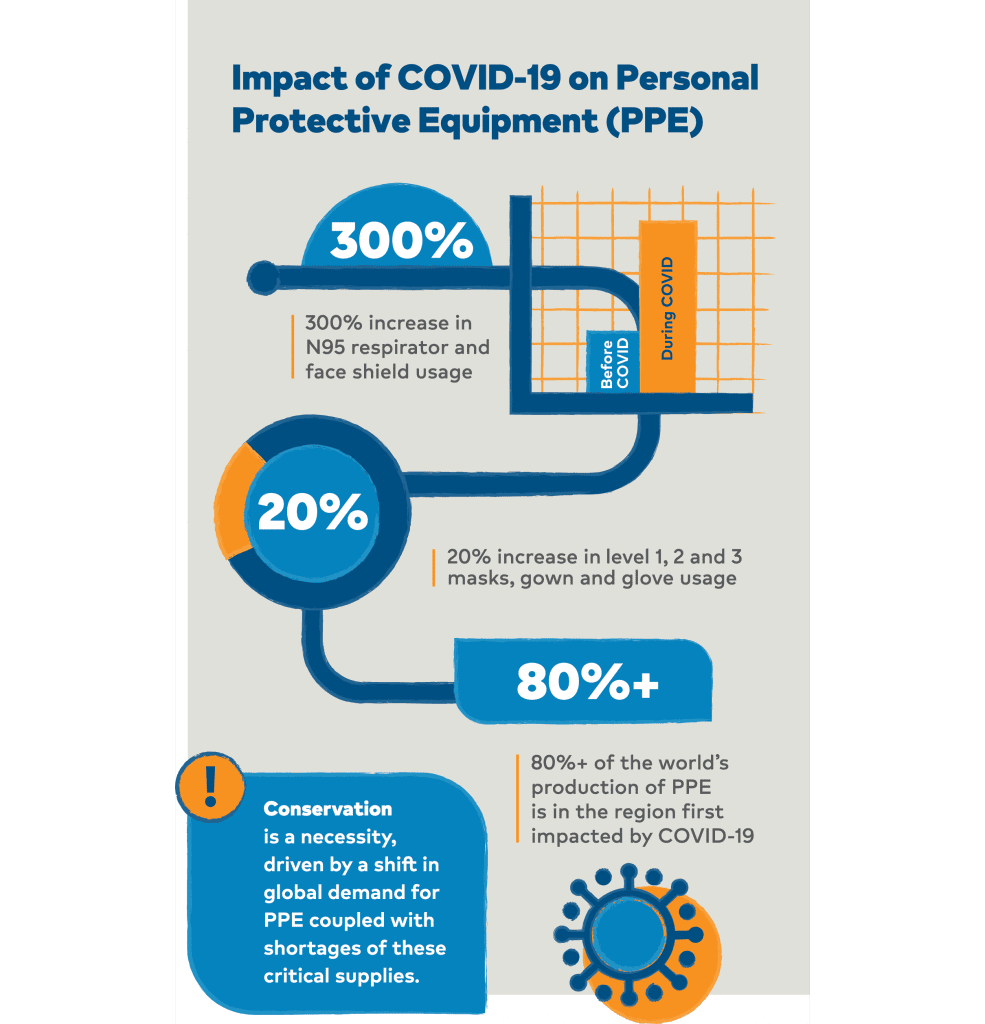
Over the past two decades, HCA Healthcare’s supply chain team has evolved to meet the needs of caregivers and patients during events as sweeping as hurricanes, floods and wildfires. Supply chain is an intricate, multifunctional service aligned with each division of HCA Healthcare to ensure facilities and staff have the supplies necessary to support high-quality care, even during a global pandemic.
It takes tremendous teamwork, organization and technology to keep supplies on hand and up to date. From surgical supplies to pharmaceuticals and disposable gloves, the system touches every aspect of facility operations. As the virus expanded globally, supply chain’s effort became one of unprecedented intensity, especially since so many products are sourced overseas and supply was threatened. From the start, this event aligned supply chain and the Clinical Services Group (CSG) more than ever before.
“That’s definitely true,” says Ron Powell, National Group Supply Chain CEO. “In the case of a crisis, supply chain becomes very much a logistics organization tasked with sourcing product and moving it around the country. Whatever the needs may be—from tents to PPE—we’re going to do everything we can to support our clinicians and hospital staff.”
During the pandemic, one link in the supply chain that’s seen an enormous amount of attention is the importance of conserving PPE—the garments and accessories front-line colleagues depend on when caring for patients with infectious diseases. “Our management of PPE has been a collaborative effort with HCA Healthcare’s Clinical Services Group to identify the appropriate uses of those products and take measures to conserve the products for sustainable use during this unprecedented event,” says Ron. “How do we, as a supply chain organization, best manage those products in light of shortages, allocations and growing demand?”
We are blessed to have all the PPE and equipment we need to appropriately care for our patients while staying protected. Our workload has increased but we have adapted, communicated and come together to provide the best care for our COVID-19 patients.— Noel Edwards, RN, BSN, CCRN, TNCC, Rapides Regional Medical Center, Alexandria, La.
Conservation
Managing PPE has been key in meeting the extraordinary demands of the pandemic, Ron explains. And it just so happens that more than 80% of the world’s production of PPE is in the region first impacted by COVID-19. Globally, demand was outpacing supply, and production stopped for about six weeks, making availability that much more difficult. “We set up a command center at the end of January when we saw that the supply line was getting tight and recognized that there were a number of things we needed to do to protect staff,” Ron says. “We started working very closely with CSG and others to review clinical guidelines and COVID-19 projections, thus informing our supply management decisions. Throughout February, we were acquiring product and setting up measures to ensure sustainability. We refined our reporting infrastructure to meet the unique needs of this event.”
Adaptability
One of the challenges of preventing weak links in the supply chain is ensuring that distributors can meet the sudden demand surge. “Hand sanitizer is a great example,” Ron explains. “Our supplier was overwhelmed by the demand, not just from healthcare providers, but the retail business as well. Our team members worked daily with our supplier to provide need projections and ensure supply was obtained. We then turned to alternate suppliers like distilleries to quickly meet the need.”
Government relations
That work-together spirit extends to one of the supply chain’s key partners: government entities, be they local, state or federal. Without their cooperation and resources, the necessary tasks would be nearly impossible to complete.
“In each state where we operate, we have a robust relationship with the government,” says Ron. “We’ve received product in most of our markets from the state stockpiles. Some of those are very highly restricted to a specific facility; others are available more for our facilities in that state, and we can move product around as needed.” Having established distilleries connections in Washington is also a good thing for supply chain operations. “HealthTrust and HCA Healthcare have been influential at the federal level as well,” says Ron, “with representation on Vice President Pence’s Coronavirus Task Force.”
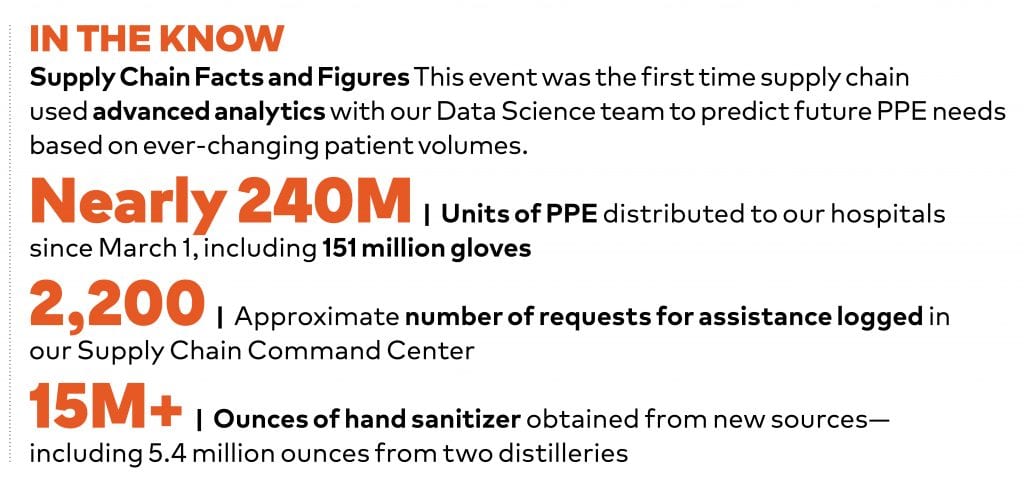
Being ready for the next phase
The COVID-19 pandemic has been devastating in more ways than one. Yet in the midst of this event, our organization has learned so much through collaboration, rapid response and a general willingness to think creatively. “We’ve certainly changed our approach. It’s not a question of if but when there’s a second round of COVID-19, because everybody’s predicting there will be,” says Ron. “We’ll be better prepared to know how we need to respond from a supply side. We’re preparing for it by projecting our future needs based on lessons learned from this first phase. We’ll be better informed as to what we really need, how hospitals will be set up and how they’ll take care of patients. This event will inform how our supply chain meets the needs of our hospitals as they reopen.”