Kimberly Wilson and her sterile processing team are the ultimate "behind-the-scenes" colleagues.
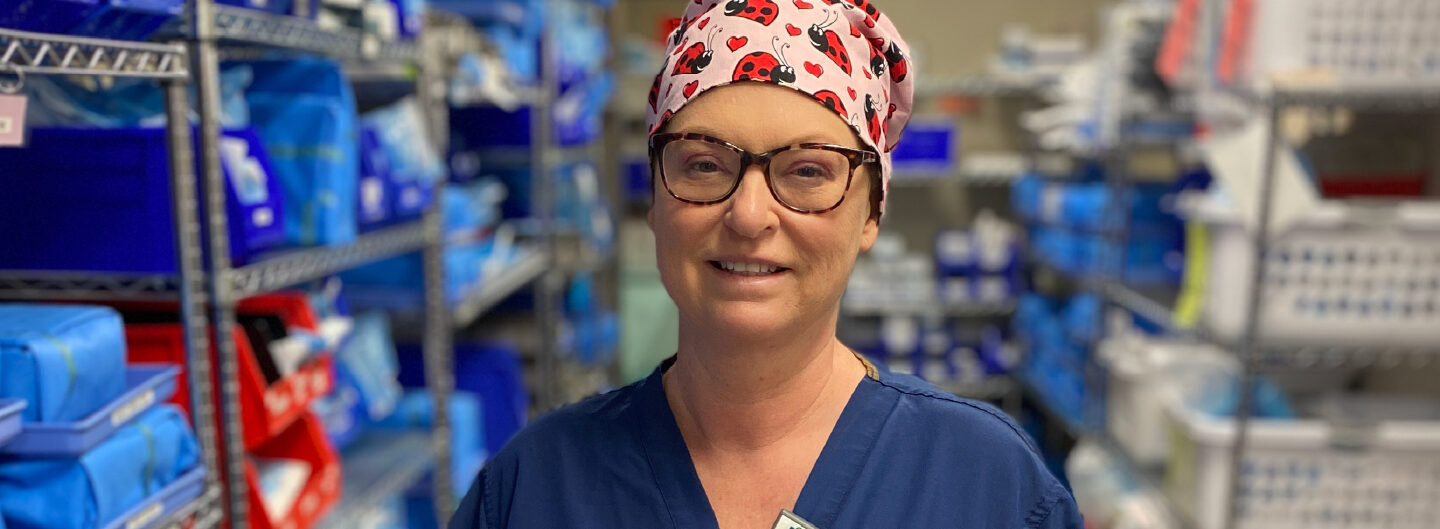
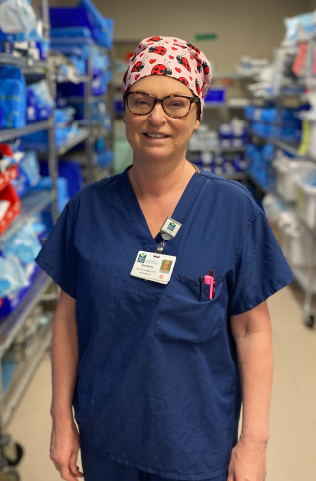
In the world of medicine, infection prevention is a top priority for surgeons and caregivers. Keeping infection at bay is also the primary responsibility of Kimberly Wilson, sterile processing supervisor at Lee’s Summit Medical Center in Missouri (LSMC, MidAmerica Division).
After earning her associate degree in applied sciences from Riverland Technical College in Minnesota, the Iowa native’s career started with a 10-year stint as a surgical technician at the Mayo Clinic. From there, she went to Creighton University Medical Center in Omaha, Nebraska, and soon joined the HCA Healthcare family.
Kimberly has been at LSMC for six years, the past two as sterile processing supervisor; where her staff of seven equips six operating rooms and several in-house and satellite clinics.
Q: In general terms, what do your responsibilities entail?
A: There are hundreds of surgical instruments and surgical sets depending on the general surgery – spine surgery, orthopedic surgery, vascular surgery – and we have different instrument sets for different surgeries. It’s our job to properly clean them in the proper soap and at the proper temperature. We start with mechanical washing by hand, and then we put them in an automated washer, almost like a dishwasher, and they come out on the clean side.
When we’re inspecting our trays, we make sure everything is clean, gets packaged up into that specific tray and goes into our autoclave – our steam sterilizer. Then we grab a count sheet and start assembling the trays back together, testing each instrument as we go to make sure it’s working properly.
We keep records of everything. All our machines get tested – our autoclaves, our soap dispensers, our washers. We run a test on everything every 24 hours to monitor that it’s calibrated correctly and working properly.
Q: What is your relationship with the surgeons at your facility?
A: There are a lot of surgeons in this facility who are very complimentary. They take our department very seriously, and I appreciate that. That also comes from my being in the OR with them. They’re not afraid to call me in and say “Hey, do you think this is OK to use?” It’s all about the patient in the OR and also behind the scenes. We always think “Would I want this used on me or my family member?”
Q: How does technology impact your work?
A: We have four surgical robots right now. The instrumentation, cameras and scopes that they use for those surgeries require a pretty intense cleaning process, making sure everything gets flushed and soaked and thoroughly cleaned and then inspected. We make sure it gets sterilized properly. We have two forms of sterilization: steam in our autoclaves and then a low-temp, hydrogen peroxide-based sterilization.
I have a natural desire to help others and be part of something bigger than me.— Kimberly Wilson, sterile processing supervisor at Lee’s Summit Medical Center in Missouri (LSMC, MidAmerica Division).
Q: Your team really touches every department, doesn’t it?
A: We are an 80-bed hospital with six ORs, and three of those ORs have surgical robots in them. We’ll work with instruments for the Cath lab, the ER and the GI lab. We also have outside clinics, like a wound clinic, that send their instrumentation to be cleaned and sterilized. We package it back up and send it out with our hospital courier. We have the pain clinic with their electrical probes that they send down to us. They’re very delicate and must be treated delicately. They’re very expensive and must be washed by hand, dried and sterilized in our low-temp sterilization cleaners.
Q: What best practices do you and your team employ to ensure your own safety as well?
A: We inspect instruments for bioburden (bodily fluids, including blood) in the decontamination room, where we are gowned up with our personal protective equipment (PPE), gloves, eyewear, all of that. Everything gets scrubbed down by hand and then put into our automated washers.
Q: The job is non–stop, isn’t it?
A: When we’re inspecting our trays, we make sure everything is clean, gets packaged up into that specific tray, goes into our autoclave, our steam sterilizer. We keep records of everything. All of our machines get tested – our autoclaves, our soap dispensers, our washers. We run a test on everything every 24 hours to monitor that it’s calibrated correctly and working properly.
Q: When considering hospitals, most patients often think of doctors, nurses and perhaps the technicians they interact with. Are you and your staff the ultimate “behind-the-scenes” workers?
A: Absolutely – it’s a very important job that not a lot of people know about. It’s nice to get word out that there are people who take pride in and show integrity in making sure that instruments are cleaned and in proper use. It’s just something people don’t think about. They’re concerned with their doctor and what they need to do before and after surgery.
Q: What are the biggest challenges of your job?
A: Right now, it’s space. I had 40 trays brought in just the other day. So we have growing pains, let’s put it that way. We need more space, but
HCA Healthcare is aware of that, and we’re on the list (for improvements). But we’re making it work.
Q: What’s most rewarding about your job?
A: I have a natural desire to help others and be part of something bigger than me. We’re definitely a team here, from the sterile processing of the instruments to using the instruments in the OR. You just have to be prepared for the unexpected. It can be a fast-paced environment. It’s an intense place to work, and it’s an intense responsibility, but I enjoy it.